一. 塑料行业在国内的发展形势
现在人们已公认一个国家或地区塑料的人均年消耗量及塑料工业在国民经济中所占的地位是反映工业发展与进步的重要标志之一。中国塑料资源丰富,21世纪初主要合成树脂年产量达1.4万吨,排世界第4位。并且中国合成树脂的产量还在以5%~10%的速度增长。中国又是塑料消费大国,据统计,其年消耗量占世界第二,仅次于美国,而中国的人均消费仅为19kg,在世界排名第32位,是工业发达国家的11%~20%,可见中国的塑料工业还要大发展,塑料机械前景广阔。根据塑料制品的市场分析,目前中国塑料机械行业产值每年约100亿元,而国内市场需求约200亿元,还有很大空间,注塑机的需求也逐步由南方向北方扩散,同时也带将带动塑料工业关联产业的发展。
二. 变频改造在注塑行业发展趋势
近几年塑料行业发展越来越迅速,其中注塑行业也正迎来一个飞速发展的机遇。但同时行业内的竞争也日渐激烈,各厂家除了重视产品质量和品牌外,也越来越重视生产成本的控制。从注塑机工艺过程知道,在注塑成型产品成本中,电能消耗成本占了很大的比例,因而能否有效减少电能损耗,受到了各注塑机厂家和用户的关注。随着变频调速技术的推广,变频调速在传动控制和节能领域已日渐得到了广泛应用,尤其在泵类负载场合采用变频控制节能效果显著。本文以四方注塑机专用型变频器为例,介绍了注塑机变频改造的可行性和改造中常出现的问题及相应处理方法。
三. 注塑机变频改造可行性
3.1 注塑机基本概况及成型工艺过程
普通注塑机通常采用液压传动,其结构包含注射装置、开合模装置、液压传动装置和电气控制装置,后者的作用是保证注塑机预定工序的要求(压力、速度、温度、时间、位置)和动作程序准确有效地工作。
在传统的注塑机中液压传动装置主要由油泵、液压控制阀、压力电磁比例阀、流量电磁比例阀、各种不同的动作油缸、油泵电机及其它液压附件和管道组成,液压传动系统中的动力由电机带动油泵提供。其中,油泵绝大部分是定量油泵,电动机通常提供额定功率和转速,油泵将电动机所输入的机械能转变为压力能,然后向液压系统的液压元件输送具有一定压力和流量的液压油,满足液压执行机构驱动负载所需能量的要求
注塑机成型工艺是一个按照预定的周期性动作过程,即以合模---射嘴前进---射胶---保压---溶胶、冷却---开模---取出制品---将被注塑件放入模具中—合模等加工工序达到某件产品成型。
各个过程所需的速度和压力因不同工艺而不同,即所需的液压油流量不同,因而注塑机整个动作过程对油泵电机来说是个变负载过程。在定量泵注塑机液压系统中,油泵电机始终以恒定转速提供恒定流量的液压油,各个动作中相应多余的液压油则通过溢流阀回流,从而造成电能的浪费。据统计,由电液阀控模式造成电能损耗高达36~68%;根据注塑机设备工艺,油泵电机耗电占整个设备耗电比例高达65~80%。因此,对阀控电液模式进行节能改造具有很大的潜力。
3.2 普通注塑工艺中的主要损耗
第一为溢流损耗。随产品及加工工序不同,各工序所需液压、流量、压力不同(见附图1)。对于油泵马达而言,注塑机在注塑过程的负载是处于变化状态。而泵的流量是按照所需的最大流量来设计的,其原注塑油泵马达以恒定的转速提供的液压流量,当注塑机所需的流量小于最大流量时,多余的液压将通过溢流阀回流,这一部分能量就损耗掉了。
第二为节流损耗。当液压油流经阀的节流口时会有一定的压降,这就是节流损耗。由于方向阀的节流面积比较大,所以大部分的节流损耗发生在比例阀上。同时由于液压长期全速循环流动与液压件机械剧烈磨擦,造成油温过高,噪音过大,机械寿命缩短等不良现象。
第三为设计余量损耗。通常在设计中,一般会考虑到共用性,设计时以最大容量为基础,因此用户油泵电机设计的容量比实际需要高出很多,存在“大马拉小车”的现象,造成电能的大量浪费。
图一:注塑机工序图和能耗对照图
四. 变频器在注塑机节能改造中的优点
4.1 调速节能
根据注塑机的工艺要求,把总压阀、低压阀、一压阀、二压阀的开关信号经转换后加在变频器的输入端作为变频器的频率给定信号,变频器通过对其进行实时采样并通过CPU处理,使输出频率随比例阀的模拟信号成线形变化,在需要压力和流量较小的工艺过程中使电机转速降低,从而降低电机的输出功率,在冷却和半成品置入过程中可以让电机停转,使电机在整个负载范围内的能量损耗达到最小程度。
4.2 提高功率因数节能
无功功率不但增加线损和设备的发热,更主要的是因为功率因数的降低导致电网有功功率的降低。由公式S²=P²+Q²,Q=S*SINφ,P=S*COSφ,其中:S-视在功率。Q-无功功率,P-有功功率,COSφ-功率因数。可知,当COSφ越大,有功功率 P越大。普通定量泵注塑机COSφ值在0.6-0.8之间,而使用变频调速装置后,由于变频器内滤波电容的补偿作用,使得COSφ≈1,从而减小了无功损耗,增大了电网的有功功率。
4.3 软启动节能
由于原电机为直接启动或Y/△启动,启动电流等于(3-7)倍额定电流,这样会对机电设备和供电电网造成严重的冲击,而且还会增加电网容量要求,启动时产生的大电流和震动对设备的使用寿命极为不利。而使用变频节能装置后,利用变频器的软启动功能将使启动电流从零开始,最大值被限制在变频器设置的加速中电流限幅水平以内,一般不超过1.7倍额定电流,减轻了对电网的冲击和对电网容量的要求,延长了设备和模具的使用寿命。
五. 变频器节能改造原理
由泵类负载的工作特性可知,泵的流量与转速成正比,泵的扬程与转速的平方成正比,泵电机轴功率与转速的立方成正比,如下述公式所示:
Q2/Q1=N2/N1 ;H2/H1=(N2/N1)2 ;P2/P1=(N2/N1)3
其中Q为流量、N为转速、H为扬程。
图2:阀门控制与变频控制节能比较
图2给出了阀门控制与变频控制两种模式下的节能效果比较。原有注塑机系统采用阀门控制,当流量由QA减少到QB时,由于管阻特性,工作点由A点转移B点,消耗的功率与0EBF的面积成正比。若采用变频控制,这时因阀门全开,其管阻特性不变,工作点由A点转移到C点,消耗的功率与0ECH的面积成正比。因此,从图2中可以看出,采用变频调速比阀门控制更加节能,且随着转速的降低,电机输出功率成立方关系减少。这样,根据注塑工艺适时地调节油泵电机的转速,即可达到节能的目的。
目前三相异步电动机大多采用变频调速,由电机同步转速公式:
n=60(1-S)f/p
其中,n为电机转速;s为转差率;f为供电频率;p为极对数。
由上式可知,改变电源频率即可改变电机转速。因此,采用注塑机比例流量阀及比例压力阀的控制信号同步控制油泵马达的变频器,使油泵电机的转速与注塑机工作所需的压力、流量成正比,从而使溢流阀的回流量减到最小,液压系统输出与注塑机生产所需功率相匹配,便可达到节能目的。据统计,其单机节电率可达25~65%。
注塑机工序过程
不论大、中、小型注塑机,分析它的工序过程是相同的,大致是五个工序过程,见图1。
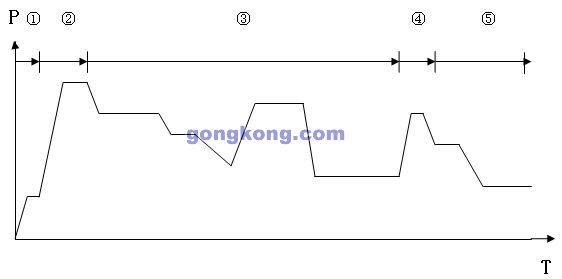
从图1可知注塑机工序过程是:
①送模具过程,需低压力,时间较短。
②合模具过程,左右两个模具相接,直至完全闭合,需略高压力,时间不长。
③射胶、保压、冷却过程,送料至模腔,直到成型,固化完需较高压力,时间长约占40-60%。
④脱模具过程,加工成型,可开启模具,到脱模完,可取出加工件,时间不长,压力略高。
⑤退模具过程,加工件取出,模具后退原位,进行辅助工作后,待再次加工,这时需低压力,时间较短。
对同一台注塑机,加工不同的塑料件,其压力(p)与时间长短是各不相同的。它与加工件的型体复杂性,使用何种塑料,一个加工件的总料量,有否嵌件等有关,具体参数设定,一般由工艺技术人员给出的,并经试验加工后,最后定案的。
3 注塑机节能的可能性分析
从图1注塑机的P=f(t)工序过程中看出,随着不同时间段,它的主油泵压力是变化的,而且起伏较大,这就存在节能的可能性,且潜力较大,所以注塑机节电率可达20%-50%,甚至更大些。在未使用变频器的注塑机,其主泵压力调整是靠压力卸荷来调节傍路油路的开度,来实现调节压力的方式,这种主泵调压力的方式,对主泵的电动机转速不变,依傍路阀门开度来调节压力,实践证明节能是很小的,还有一种使用变量泵的注塑机,节能效果达百分之十几,但设备维护成本较高,泵容易损坏,因此也不是经济的运行的方式,采用变频器调速来调节主泵的转速,从而改变流量和压力是较经济的运行方式(这时阀门的开度要全开
100%),这就是注塑机主泵采用变频器的原因所在,从而有较大幅度节电的道理,至于模具移动的动力源也是液压的,它有二种方法:
①另配一台小功率的低压油泵。
② 由主泵分路经减压阀作动力源
又关于各段时间的定位控制,常见的有四种方法:
① 依靠移动平台的滑杆,用行程直接点
开关(小型的)
② 依靠时
继电器定时控制(中型的)
③ 依靠单片机或
PLC控制(大型的),我公司的方案即如此。
④ 利用变频器本身多段速度与时间的控制(小、中型的)。